The equipment installation Qualification checklist is the tests performed during IQ, which prove equipment installation according to the design requirements and manufacturer’s recommendation. Let’s discuss what to include in an Installation Qualification checklist.
Equipment Installation Qualification is part of equipment validation activity, performed after the equipment is installed. It consists of an equipment installation qualification checklist that verifies the equipment’s installation according to the design and manufacturer’s recommendation
It provides documented evidence that the pharmaceutical equipment is installed according to the equipment’s design requirements and the manufacturer’s recommendation. Additionally, after installation, the equipment will operate and perform as per the buyer’s requirements.
These requirements and recommendations are thoroughly discussed during the design qualification phase.
Equipment Installation Qualification template
The equipment installation template is the format used to record all tests during the Installation qualification activity. It presents a checklist sequence, followed by personnel during the IQ activity.
There are no strict rules and regulations for designing installation qualification template, and it mainly depends on the manufacturer and the buyer’s decision. However, a typical installation qualification template consists of a test description, its acceptance criteria, and the actual result.
Tests are written in tabular form, with their corresponding acceptance criteria, actual value, and result, i.e., Pass or Fail.
When a particular set of tests have been conducted, the person conducting the IQ signs it, and the quality person approves the test by its signature.
The common Installation Qualification format is mentioned below.
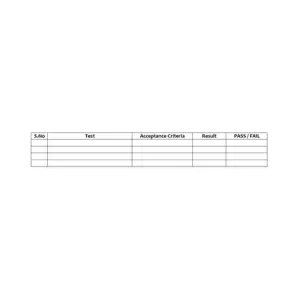
In the above template, below is the explanation of each column
- Test: it is a parameter under test during the IQ activity
- Acceptance Criteria: The recommended result of the test on which the IQ test is considered satisfactory.
- Result: The actual outcome of the test being conducted
- Pass/ Fail: Whether the test is a fail or pass, depending upon the test outcome
Equipment Installation Qualification Checklist
Installation Qualification checklist is a series of tests performed related to equipment installation. Before conducting Installation Qualification, the manufacturer prepares the desired IQ checklists in an approved format. These checklists are then sent to the buyer for their review and approval. When both the manufacturer and buyer approve the test format, the Installation Qualification checklist becomes official.
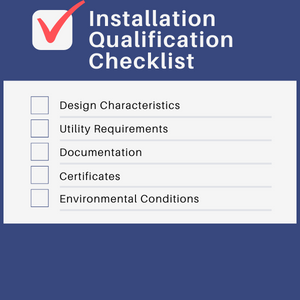
Let’s look at common tests routinely performed in an Installation Qualification activity.
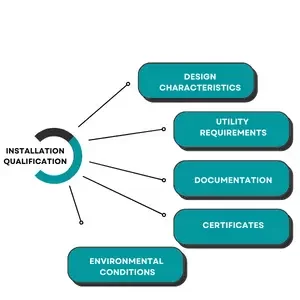
Design Characteristics
It includes tests related to the design attributes of the equipment being installed. It ensures that all the attached components are installed according to the agreed characteristics.
Let’s look at some design characteristics tests and their acceptance criteria.
S.No | Test | Acceptance Criteria | Result | PASS / FAIL |
1 | Material of construction
Piping Exhaust Electrical Conduit Pneumatic Conduit Duct |
SS / MS / Insulation MS SS / MS SS / MS SS / MS |
||
2 | Area of Installation | The area must be free from dust and particles | ||
3 | Ventilation | There must be adequate arrangements of ventilation in area | ||
4 | Foundation | The equipment foundation must be solid and rigid | ||
5 | Space for person movement | Adequate space for the operator and another personnel movement must be provided | ||
6 | Space for material | Adequate space for placing different material must be provided | ||
7 | Electrical safety | The electrical supply must be properly provided with relevant safety system | ||
8 | Compressed Air | The compressed air must be supplied with adequate pneumatic components and safety system | ||
9 | Steam Line | The steam line must be proper with adequate components and safety system |
Utility Requirements
This section verifies that the utilities provided are according to the equipment requirements, as agreed during the design qualification phase.
Every pharma equipment requires standard utility supplies for its satisfactory performance. The equipment will not operate according to design specifications if these are not provided.
Some tests common in this section are mentioned below.
S.No | Test | Acceptance Criteria | Result | PASS / FAIL |
1 | Electricity | The electrical supply must be
· 380V/220 VAC · 3 phase / single phase |
||
2 | Steam | The steam pressure must be _____ bar / psi | ||
3 | Compressed Air | The compressed air must be ___bar / psi.
The compressed air must be dry, free from water. |
||
4 | Natural gas | The natural gas pressure must be——– bar / psi. | ||
5 | Chilled Water | The chilled water supply must be ——– bar / psi, at ——–⁰C | ||
6 | Purified Water | The purified water supply must be ——– bar / psi. | ||
7 | Water for Injection | The water for injection supply must be ——– bar / psi. |
Documentation
During the design qualification phase, the buyer mentions the documentation they require, which becomes mandatory for the manufacturer to supply with equipment.
In this test, the buyer checks and verifies all the required documentation that the manufacturer has supplied with the equipment.
Some common tests performed in this section include the following.
S.No. | Test | Acceptance Criteria | Result | PASS / FAIL |
1 | Operation Manual | Operational manual with detailed guidelines should be supplied | ||
2 | Wiring Diagram | Wiring diagram with detailed guidelines should be supplied | ||
3 | Maintenance manual | Maintenance manual, containing schedule with detailed guidelines should be supplied | ||
4 | Validation documents (including DQ, IQ, OQ and PQ) | Manufacturer must provide following Validation documents
IQ OQ PQ |
||
5 | Preventive Maintenance Manual | Manufacturer must provide Preventive maintenance procedure with complete schedule | ||
6 | Calibration | Manufacturer must provide calibration procedure of all measuring instrument and devices with detailed schedule. | ||
7 | Spare parts list | Manufacturer must provide spare parts list of all the critical items and components. |
Certificates
This test includes verification that the desired certificates are provided with the machine, agreed upon during the design qualification stage.
Certificates are necessary because the pharma process are critical and requires specialized materials, devices, and instruments. To ensure that the manufacturer has adequately applied all requirements, the manufacturer provides certificates as proof. Additionally, regulatory authorities such as the United States FDA can review them during their routine inspection.
Some common tests performed in this section include the following
S.No | Test | Acceptance Criteria | Result | PASS / FAIL |
1 | Calibration certificates | Calibration certificates for all the recording and measuring devices must be provided
The certificates must not be expired |
||
2 | Material of construction
|
Certificates for material of construction of specific machine parts must be
Product contact parts must be SS 316L Non contact parts must be SS 304 |
Environmental Conditions
In this section, environmental condition equipment is checked and verified.
Pharmaceutical equipment require specific conditions for their satisfactory performance. If the desired environmental conditions are not provided, it will negatively impact the output product and equipment performance.
Some common tests performed in this section include the following.
S.No | Test | Acceptance Criteria | Result | PASS / FAIL |
1 | Area Temperature | The temperature must be—– ⁰C | ||
2 | Area Humidity | The area humidity must be ——– | ||
4 | Laminar Flow | Laminar air flow with —– air speed must be installed | ||
5 | Air Changes | Air changes in the area must be —- | ||
6 | Differential Pressure | Differential pressure of the area must be——-
The pressure in the areas must be negative / positive |
||
Area Classification | The area for production must be ___ (Class A , B , C , D) |