A pharmaceutical tablet press is used to produce tablet form of dosage, in solid dosage processing. Learn the working principle of pharmaceutical tablet press and its different parts.
A pharmaceutical tablet press is used to produce tablets form of dosage in the pharmaceutical industry. It compresses the powder with high force and pressure until it becomes solid and rigid. The tablet acquires its properties during compression, and after compression, it comes out of the machine for further processing.
The infeed powder is a composition of raw materials having the desired therapeutic effects, which is usually in the form of granules and processed through fluid bed dryer mechanism
The powder is fed into the machine hopper, then travels through different components into the die. In it, the powder is compressed through upper and lower punches. The force exerted by the set of punches gives tablets their required physical and therapeutic effects.
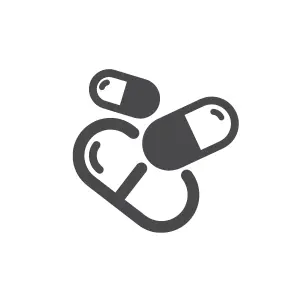
The pharmaceutical tablet press is an integral part of Oral Solid Dosage processing equipment in the pharmaceutical industry. Every pharma industry has a dedicated tableting department for producing tablets. Additionally, the tableting department has dedicated resources such as HVAC, Personnel, and Building.
Working principle of pharmaceutical tablet press
The working principle for the pharmaceutical tablet press machine can be described in the following steps
- Filling
- Weight Adjustment
- Compression
- Ejection
Let’s discuss each step briefly
Filling
The filling is the first step in tableting, where powder or granules are filled in a hopper. The hopper can be filled manually or through the automatic mechanism.
Personnel or the operator manually fills the hopper through a Stainless Steel pharmaceutical equipment or container in a manual system.
In an automatic system, the powder is automatically transferred through a vacuum from a pharma bin. The pharma bin is connected to the tablet press hopper, and a sensor in the hopper continuously monitors the powder level. When the powder level goes below the threshold level, the main controller starts the vacuum to transfer the powder inside the hopper. When the hopper is filled up to the upper threshold level, the sensor senses, and the main controller stops the vacuum. This cycle is repeated during the entire production process.
The tablet takes the shape of a die, which is made according to the tablet’s requirements. If the powder is not appropriately filled in a die, the tablet will have varying specifications, and the quality department will reject it.
Wight Adjustment
After filling, Weight adjustment is the next step in a tablet press machine. The tablet’s weight is directly proportional to the quantity of powder in a die. The tablet’s weight will increase if we increase the amount of powder in a die. Similarly, if the amount of powder in a die is decreased, the weight will also decrease.
The position of the lower punch controls the Quantity of powder in a die. The punch moves lower to create more space in a die, increasing the powder quantity and, eventually, the powder weight. Similarly, the punch moves upward to reduce the space, decreasing the powder quantity and tablet’s weight.
There are two methods of moving the lower punch – Manual and Automatic
- Manual Method: The machine operator moves the lower punch through different levers and knobs. The operator checks the tablet’s weight through a weighing scale and increases or decreases the lower punch’s position to compensate for the tablet’s weight.
- Automatic Method: In the automatic method, the lower punch is automatically controlled through the main controller to adjust the tablet weight. The main controller continuously monitors the weight through the load cell and compares it with the required tablet weight. If it needs adjustment, the lower punch automatically moves up or down.
Compression
Compression is the main process through which tableting takes place. In this stage, powder in the die is compressed by upper and lower punches, ( part of tooling in compression) against each other. When the powder is compressed, it changes the powder’s characteristics and converts it into tablet form.
In the compression stage, two properties of tablets are adjusted – Hardness and Thickness.
For hardness, pressure is used. Higher the pressure, higher the hardness, and vice versa.
For thickness, the distance between upper and lower punches defines the thickness. Tablet thickness increases as the distance between punches increases. Similarly, tablet thickness decreases as the distance between punches decreases.
Ejection
Ejection is the final stage in the tableting process. In this stage, the tablet comes out of the die and drops into the machine discharge for collection.
For tablet ejection, the upper punch moves upward from the inside of the die. At the same time, the lower punch moves slightly upward to push the tablet from the die. When the tablet comes out of the die, a metallic assembly called Ejection Scrapper guides the tablet into the discharge chute, which drops the tablet into a collection bin or point.
At the ejection point, a sensor is installed for counting the tablets. When a tablet passes in front of the sensor, the main controller increases the count and displays it on display. The tablet count is used for batch record purposes.
Types of pharmaceutical tablet press
There are two main types of tablet press machine
- rotary tablet press machine
- single punch tablet press machine
Let’s discuss each type of tablet press machine
Rotary pharmaceutical tablet press
Rotary tablet press machines or multi-station are designed for large-scale production processes. They have multiple tooling in compression (i.e., upper and lower punches) and can produce more tablets and operate at high speed.
A rotary press includes automatic weight, hardness adjustment, auto lubrication, and rejection systems. These machines can also produce tablets at higher speeds, i.e., 1,000,000 tablets/ hour.
Single punch pharmaceutical tablet press
A single-station tablet press is a smaller version of a full-scale tablet press. It has only one station in the entire turret and contains only one set of tooling, i.e., upper and lower punches.
Single-station presses are simple and easy to operate. It does not include complex functions. Most activities, such as Tool adjustment and oiling, are performed manually.
Single-station tablet press machines are used for producing small-scale batches such as pilot batches or test batches. For large-scale production, a single-station machine is not suitable.
Pharmaceutical tablet press parts
A tablet press machine is a complex mechanical structure with many critical parts. All these parts must perform correctly and synchronize with each other to produce the tablets of the required specifications.
Some critical parts of the tablet press machine include the following
Hopper
Powder or granules are transferred to the hopper for tablet processing by a tablet press machine. Hopper is the first part of the tablet press machine to which pharma product comes in contact with the tablet press.
It releases a controlled amount of powder for the later stages of the tablet press machine.
Hopper is made of stainless steel pharmaceutical grade because pharma product (powder) comes directly with it. Some hoppers also include a manual mechanical valve to control the powder flow.
Feeder System
Powder from the hopper enters the feeder system. The primary function of the feeder system is to feed the powder accurately into the dies of the tablet press machine and ensure even filling.
Because a tablet press machine runs at high speed, some die can be left un-filled or partially filled. This condition alters the tablet’s characteristics, such as weight or hardness. Additionally, powder with high viscosity also requires more force and traction to move and fill into dies.
Inside the feeder, there are peddles that continuously rotate. As these peddles rotate, the powder underneath is moved into dies, fills up to their capacities, and excess powder remains in the feeder. Peddle rotation can be increased or decreased depending on the powder characteristics.
Punches
Punches are thin stainless steel pharmaceutical grade rods having tablet-specific designs. They are combined with two punches — one for the upper portion and another for the lower portion of the machine. Both punches are positioned with dies.
These punches move up and down at specific times during the tableting operation. Upper punches come down, and lower punches come to the upward position after the powder fills in the die. Punches exert force on the powder against each other in the die.
As the punch exerts force on powders in the dies, tablets take the shape of punch heads.
Dies
Dies are a block, usually made up of Stainless Steel, and have a bore in them. During operation, powder fills in the bore and defines the shape and size of the tablet.
The outer diameter of the die depends upon the size of the hole in the turret. When the die is placed in the turret, it remains fixed with a screw tightened across it.
Turret
The turret is a circular part that rotates during the production process. The entire tableting process occurs as it rotates, and when it stops rotating, the tableting process stops.
The turret contains bores in which dies are fixed. The bores in the turret must be aligned with upper and lower punches.