Compressed air in pharmaceutical industry is the environmental air, pressurized to a certain level higher than the atmospheric pressure. It remains at this level until delivered at its target location or point. The air used for compression is the same as breathed by humans, used without filtration and treatment by any chemical.
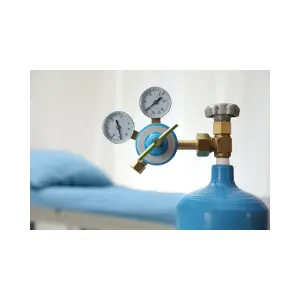
Compressed air is a critical and most frequently used utility. It acts as a driving force for the pneumatic components used in various instruments, equipment, and accessories in the pharmaceutical industry.
As the air is compressed, it stores energy in it, and when released, energy is transferred to the attached system, such as pneumatic cylinders and air motors. The pressurized air is stored in a metallic container attached to air compressors called storage tanks. The attached tank releases the stored air on a need basis.
The compressed air is pressurized, indicated in psi or bar. It must be high enough to overcome losses in the line and provide the required pressure for the process or system.
Compressed air is generated by equipment called Air Compressors. Its main components are a compressor and storage tank. The compressor takes input air from the environment and compresses it to the required pressure. As the air is compressed, it is stored in the storage tank.
Importance of compressed air in pharmaceutical industry
In the pharmaceutical industry, compressed air is used for activating pneumatic components, which are used for driving and activating various processes and applications. Some common examples of compressed air in the pharmaceutical industry include the following.
Activating Pneumatic Components
Pneumatic components are common in almost every pharma equipment and perform essential functions such as process control, safety, driving attached systems, and controlling fluid flow. Pneumatic components for these applications require compressed air to activate and control. The compressed air must be of the necessary pressure. Otherwise, it will either not operate or its response time will decrease.
For example, some steam autoclaves are supplied with pneumatic cylinders to control the door. These cylinders require compressed air of specific pressure to activate and hold the door operation.
Container blowing
Container blowing is a technique employed before filling of oral liquid dosage form for its respective containers. In this application, compressed air is blown into an empty container for a fixed time to remove foreign particles and objects from the container. After this process, the containers are transferred to the filling station, and the machine used to carry out this operation is called Bottle Blowing Machine.
In another application, the air is blown into ampoules/vials to remove the moisture or traces of water inside after washing. The machine used to carry out this function is called Ampoule / Vial washing machine, and blowing is included as a separate cycle. Its cycle starts after the ampoules/vials have been washed in their respective station, and some traces of water or moisture commonly remain inside the ampoules/vials.
Cleaning purposes
Compressed air is used as a part of the cleaning mechanism in the pharmaceutical industry to clean pharma equipment, tools, areas, and other items after the completion of each batch or at the end of the production cycle. Compressed air removes product traces, any packaging material, and other things that can be physically removed or displaced. After using compressed air, other methods, such as water and cleaning agent, are applied.
The air gun is used to apply compressed air for cleaning purposes, which is manually controlled, handheld, and can be easily aimed at the target point.
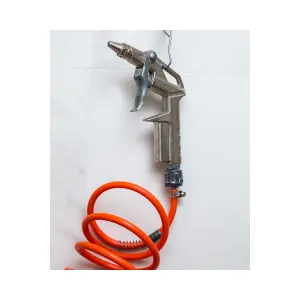
Compressed air is also used in the Clean in Place – CIP system for drying purposes, to dry the equipment, and remove the traces of moisture.
Atomization
Compressed air is used in spray guns for atomization purposes. It is a process of drop formation in a spray gun, which is critical for the success of the coating process.
In atomization, compressed air combines with the liquid being sprayed to develop a spray pattern; the spray pattern can be varied by changing the compressed air supply according to the process requirement.
Breaking vacuum
Vacuum Breaking is making an vacuum chamber at normal pressure. In pharmaceutical equipment, a vacuum is created for various process requirements. For example, the autoclave chamber is made negatively pressurized before applying steam.
Compressed air breaks the vacuum by supplying a negative pressurized chamber. As the compressed air enters the chamber, it reduces the amount of vacuum until an equal amount of compressed air is supplied to the chamber.
Air Motors
Air motors are specially designed motors that require compressed air to operate. Air motors have many advantages over other motors, but the main reason for using them is their safety in hazardous areas.
In pharma processes, areas, applications, instrument, and equipment, it is common that areas surrounding the equipment is humid and contains a high degree of moisture. Additionally, some pharma processes require alcohol for various purposes, and being volatile, its fumes are often found in the surrounding. The presence of moisture or alcohol in the air can become hazardous for electrical equipment, components, and parts and can result in electric shock or damage.
Air motors are used in pharma equipment with a high risk of electrical damage due to these chemicals and moisture. It replaces a normal electric motor and can efficiently perform the required task without affecting performance.
For example, in a mixing vessel, a product containing alcohol is mixed. Air motors are used to rotate the mixer. It helps to prevent the dangers of electrical shock, damage, and fire.
Properties of compressed air in pharmaceutical industry
As discussed above, compressed air frequently comes in direct contact with pharma products and critical processes; it must be able to prevent contamination and damage and cause any change in pharma products. This can be only ensured by a pharma-grade compressed air supply.
For the pharmaceutical industry, an effective way of ensuring a compliant compressed air is by following ISO Standard 8573.
This standard has nine parts, and part 1 determines the purity classes for compressed air for common contaminants such as particles, moisture, and oil.