Stainless steel used in pharmaceutical industry is the required material for pharmaceutical equipment. It is durable and resists corrosion and chemical reaction. This article discusses Stainless steel in the pharmaceutical industry, its type, and some key advantages.
The stainless steel used in pharmaceutical industry is widely used for manufacturing pharmaceutical equipment. It resists chemical reactions, corrosion, and reaction with the pharma product. It is also easy to clean and difficult to degrade and sustains various natural phenomena such as high temperature, pressure, and severe environmental conditions.
Additionally, regulatory bodies such as the United States FDA and the ISO require pharmaceutical product manufacturers to comply with stainless steel regulations.
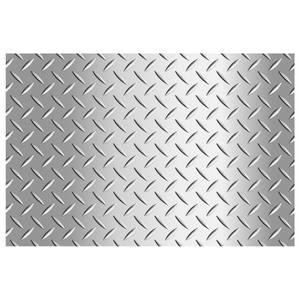
Stainless Steel
Stainless Steel used in pharmaceutical industry, is an alloy of iron in which different materials are added. The main purpose is to increase the strength of iron and make it resistant to different naturally occurring phenomena such as corrosion and rusting. The increased strength and resistance make stainless steel ideal for critical industries such as Food, Beverages, and Pharmaceuticals.
Different alloys of stainless steel contain materials with varying compositions. Some alloys of stainless steel standard in various industrial applications include the following
- Ferritic
- Austenitic
- Martensitic
- Duplex
Stainless Steel used in pharmaceutical industry
Not all stainless steels are qualified and allowed in the pharmaceutical industry. Instead, the Austenitic (often called Grade 300) type is the stainless used in the pharmaceutical industry. The main reason is that its composition makes it suitable for manufacturing pharma equipment. The Austenitic type is less reactive to pharma products and does not absorb pharma products in any form.
Environmental conditions also have minimal effect on the Austenitic type. Additionally, the chemical composition of a pharma product also does not affect the Austenitic Stainless Steel.
Austenitic types are frequently used in manufacturing pharma equipment parts that come directly with the product, like piping, fittings, Pharmaceutical vessels, hoppers, and tubing.
Two types of Austenitic are used in Pharmaceutical applications – SS304 and SS316.
Stainless Steel 304 and Stainless Steel 304L
Stainless Steel 304 is the most frequently produced and least expensive stainless steel. It consists of around 18% chromium and 8% nickel. A variant of SS304, SS304L, has low carbon composition, up to 0.03%.
The low carbon composition helps in minimizing the carbide precipitation effect. It is an effect that occurs during high-temperature processes such as welding. Carbide precipitation degrades the internal molecular structure, making stainless steel vulnerable to environmental conditions.
SS304 is not capable of providing resistance against corrosion due to chlorides and acids. For this purpose, SS 304/304L is used to manufacture equipment parts that do not directly contact with pharma products.
Stainless Steel 316 and Stainless Steel 316L
Stainless Steel 316 is a form of SS 304, with the difference that it contains 2% to 3% molybdenum. Adding molybdenum makes the SS resistant to chloride corrosion, which can damage the passive layer of stainless steel. Damage to the passive layer on stainless steel can result in the pitting of the material and can eventually make the material hazardous for a pharmaceutical product.
Another variant of SS316, SS316L, is used in pharmaceutical equipment. The L represents a variant of SS316 with low carbon concentration. The low carbon concentration is compensated by adding more quantities of Nickel. Low carbon composition enables the SS316 for applications requiring high temperatures, such as sterilization processes. The addition of Nickel allows and facilitates the SS316L to have more resistance than the non-nickel grade SS316.
SS316L can provide suitable resistance against corrosion due to chlorides and acids. For this reason, SS316L is mainly used in manufacturing pharma equipment parts that come directly with pharma products.
Advantages of stainless steel used in pharmaceutical industry
Let’s look at some benefits of stainless steel for the pharma industry
Corrosion Resistant
The significant advantage of stainless steel is that it provides excellent resistance to corrosion. The main reason is the addition of chromium. Corrosion is a normal behavior of iron when exposed to the environment, chemicals and water.
SS316L also contains molybdenum, which provides resistance to acids and industrial-grade chemicals.
Resistance to High Temperatures effects.
Stainless Steel 304L and 316L resist degradation due to processes that require high temperatures, such as welding.
The low-carbon versions of Stainless steel prevent the carbide precipitation effect, which occurs at high temperatures. Carbide precipitation degrades the material composition and makes it vulnerable to environmental exposure.
Contamination Control
Stainless steel is highly proficient in contamination control, a critical issue in the pharma industry.
The surface finish of stainless steel is highly smooth, which makes it easy to clean, and difficult for foreign bodies or microorganisms to reside on its surface material.
Easy Cleaning
The stainless steel can be easily cleaned without specialized equipment, chemicals or solvent. Simple cleaning measures can be employed for effective cleaning. The cleaning can also be performed without any specialized training.
Anybody proficient in pharma material, equipment, and product can perform cleaning activities.
Easy Maintenance
Stainless steel offers excellent resistance to corrosion caused by high temperatures. This makes it easy to perform maintenance activities because major maintenance activities require higher temperatures, like the welding process.
The high temperature for most materials is unsuitable and can result in material degradation and change the material composition. Stainless Steel, on the other hand, can be safely used for all maintenance activities.
Examples of stainless steel used in pharmaceutical industry.
Let’s look at some examples of equipment that uses stainless steel in the pharmaceutical industry.
Hopper for various equipment
Hopper is a section of pharma equipment that contains the pharma product at the initial stages of the production process. Pharma product first goes into the hopper, from where it is sent to the desired pharma equipment section or station.
The hopper comprises stainless steel 316L because it contains pharmaceutical products. Example of pharma equipment at which a hopper is used includes Pharmaceutical tablet press, Vial Capping machine, and Blistering machine in pharmaceutical industry
Piping in Water Treatment Plant
A pharma water system generates purified and distilled water for various pharmaceutical processes. Water is a basic raw material in the pharma industry and directly becomes the main constituent of most pharma products. To produce water with a high degree of purity, the entire water equipment structure, including piping, comprises Stainless Steel 316L.
Piping is mainly used for different interconnecting sections of the pharma water system. It is also used in distribution networks from water treatment plants to various departments in pharma facilities.
The piping material of construction is Stainless Steel SS316L, and it ensures safety during entire stages of water production up to its final distribution. SS316L also helps in contamination control and prevents change in water specifications until it is used in pharma product
Wheels for movable equipment
Portable equipment, such as pharma vessels and pharma bin, frequently require movement due to their need at different locations. Movement occurs with the help of wheels made of stainless steel. The stainless steel used is 304, which helps keep the process safe by ensuring a safe environment. SS 304 also prevents the corrosion of wheels and keeps the surroundings safe.
Equipment Protective cover
Various parts of equipment require a protective cover. Such parts include an electrical panel, machine back panel, and conveyor belt. Since these parts come near the manufacturing process, these parts must be good at contamination control, corrosion resistance, and provide the highest degree of cleanliness.
This can be achieved by using stainless steel for manufacturing these parts. Since the product does not come in direct contact with these parts, SS304 is used.