Surface finish describes the metal’s surface characteristics used in pharma equipment, machine and instruments. This article discusses surface finish requirements for pharmaceutical equipment
Surface finish requirements for pharmaceutical equipment
The pharmaceutical industry is characterized by stringent quality, safety and regulatory requirements in product manufacturing. These requirements span through various components, such as cleanliness, area , raw materials and many more. Surface finish is also one of many, that define the compliance requirements for metallic surface of equipment, instruments and other components. Every components that are used in critical processes must fulfil specific surface finish requirements for product safety and quality.
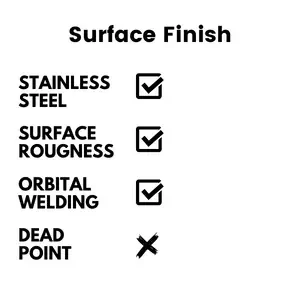
What is Surface Finish?
Surface Finish is the nature or physical condition of the outer surface of the material, and it is the function of many factors, such as roughness, waviness, lay, and coating. It describes the pattern on the surface, and overall appearance of the metallic surface.
The surface finish is described in different variables, each of which must remain within the acceptable limits, to be able to use in pharma grade processes and applications.

What are the GMP requirements for equipment used in pharmaceutical production?
Surface finish is the major requirement for pharma industry, and must be within the limits, to prevent product & metal contamination and degradation due to the metal surface. It also serves as a regulatory requirement for the pharma industry.
For the pharma industry, there are no specific conditions regarding surface finish. However, the FDA guideline 21 CFR 211.65(a), provides some basic guide on the type of equipment construction. According to the FDA surface finish requirements, “Equipment shall be constructed so that surfaces that contact components, in-process materials, or drug products shall not be reactive, additive, or absorptive so as to alter the safety, identity, strength, quality, or purity of the drug product beyond the official or other established requirements.”
Always mention Surface finish requirements for pharmaceutical equipment when buying a new equipment
Since it is mandatory compliance and safety requirement, the equipment buyer must mention this requirement before buying new equipment or system. Commonly, User Requirement Specification – URS is a standard document which includes all the equipment, process, area and other relevant data for equipment manufacturer to include into the equipment.
The main reason for specifically including is that, surface finish is achieved by using high quality & graded materials, such as Stainless Steel. Moreover, it also requires costly processes, which significantly adds the costs to the overall equipment price. If a buyer does not include these specifications, then chances are that the equipment manufacturer can use any other non-compatible material. This will, in turn, be bad for the equipment buyer, with nothing to claim.
What are surface finish requirements for pharmaceutical equipment?
Let’s discuss surface finish requirements for pharmaceutical equipment
Stainless Steel
Stainless Steel is the most important requirement for product contact parts in the pharma industry. All the critical parts that come in direct contact with the product must be made up of Stainless Steel.
The biggest advantage is that It withstands reactions with chemicals such as active pharmaceutical ingredients – API used in manufacturing a pharma product. Additionally, Stainless Steel also resists the corrosion in metals.
Many variants of Stainless Steel are developed for the pharmaceutical industry. ,The degree of contact with the product defines the stainless steel selection, and are SS316 and SS316L
SS316
For parts that comes direct contact with product is called Austenitic series of Stainless Steel, 316. This type has high chromium, nickel, and molybdenum, which makes it more corrosion-resistant, while molybdenum makes it resistant to acids, alkalis, and chlorine.
SS316L
A variant of SS316, called SS316L, has become more common in pharmaceutical applications. It contains low carbon content, so it has the letter ‘L” at its end. This variant of SS is more resistant to contamination.
In addition, SS 316L can also be used in processes requiring high temperatures, such as Autoclaves (where high autoclave temperatures require specialized material for product contact parts), and Dry Heat Sterilizers, because it has a low carbide precipitation effect.
Surface Roughness
Surface roughness is the measure of variation in the height of a metallic surface. Although the surface can look smooth to the naked eye, it can have height variations.
The rough surface, if used for pharma application can pose the following risks.
- Facilitates microorganisms and bacteria to stick or attach to the surface, making them difficult to remove.
- Can be easily subject to wear and tear. It can easily alter the material characteristics and cause a hazard for pharma products and processes.
- Difficulty in cleaning. Tiny bacterial or microbial contaminants can easily reside on irregular surfaces, making cleaning methods ineffective.
Surface roughness is a numerical value, which represents the degree of roughness of a surface. Higher the value, the more a surface is considered rough and vice versa. The symbol for Surface Roughness is Ra.
For pharmaceutical applications, the recommended values are less than 0.8. Any material with a surface roughness of less than 0.8 can be safely used for pharmaceutical production processes.
Orbital Welding
Welding is used to join two metals during machine manufacturing using high temperatures. However, the high temperature degrades the material and disturb its surface, which is a major disadvantage for pharma applications.
To counter these disadvantages, there is a specific welding, called Orbital is approved type for pharma industry applications.
Orbital welding welds a tube by rotating the weld head 360⁰ around the tubing. The welding operation is automated and controlled by a main controller. It uses a Tungsten electrode and an inert gas, commonly, argon, as an arcing agent. The inert gas is filled between electrodes, which rotates across the tubing diameter. As the electrodes rotate, the arc continues, until it completes the entire rotation.
The benefit of orbital welding is that its welds are consistent, without any dead points from the internal and external of the joint. Consistency can be ensured around a full revolution, and results in a smooth surface finish.
Another major advantage of orbital welding is that there is a minimum or no change in surface characteristics, which is a common disadvantage in other welding types. This feature prevents change in surface roughness values, and the resultant microbial growth and contamination.
Dead points
Dead points are the isolated points on a material surface of piping, tubing, or a metallic surface. It can trap any substance that passes over or reaches it. Liquid can easily trap in dead points and becomes hazardous for pharmaceutical products and processes. The trapped liquid in the dead point facilitates microorganism growth and causes contamination in the pharma production process.
These dead points are difficult to clean and sanitize because these are isolated places, and it becomes difficult for the cleaning agent to reach, and remove the contaminants.
ASME – BPE standards, known as Length to Diameter L/D ratio, are used to represent dead points in the material. It suggests that for pharmaceutical applications, the L/D ratio should be less than 2
Want to hire me for your writing tasks, click here