Like pharma drug manufacturing, API manufacturing is a critical process and requires various necessities such as manufacturing facilities, quality testing, and other related. Among other requirements is the API manufacturing equipment that performs all the processing.
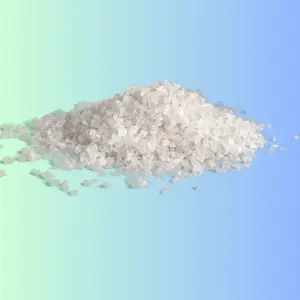
Active Pharmaceutical Ingredients are active in pharma drugs, producing the desired therapeutic effects. Without the API, pharma drugs will only act like a mixture of chemicals without any purpose. There are various ways to manufacture an API. Still, commonly, these are extracted from natural resources and chemically synthesized, the selection of which depends on the type of API being used.
API manufacturing equipment
Some common API manufacturing equipment used in API manufacturing are described below
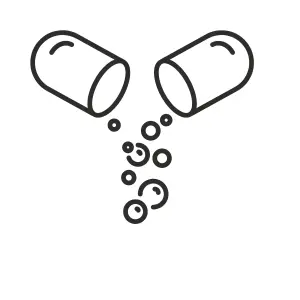
Reactor
A reactor is a type of vessel made up of metallic, typically Stainless Steel – SS316L, because of its immunity to corrosion, degradation, and reacting with the product inside. It also contains accessories such as temperature monitoring systems, gauges and various indicators. Their main purpose is to monitor the manufacturing process and chemicals inside.
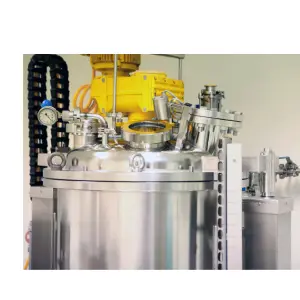
Reactors are mainly used for reactions between chemicals by mixing a liquid chemical with another liquid or a liquid chemical with a solid. Some reactors are provided with an agitator or mixer driven by a motor for the mixing process.
One of the features of these reactors is the temperature control system to provide a specific temperature. Because, in API manufacturing, some chemicals require specific temperatures to react and produce the desired results.
Some accessories related to reactors include, but not limited to
- Inlet for supplying utilities
- Ports for various sensors
- Nozzles
- Manhole
- Glass view
Filtration
Filtration equipment is used to separate impurities from the product. Examples of impurities include starting material, reagents, catalysts and by-products.
Filtration passes liquid through a filtration assembly containing the required filter. As the liquid passes through the filter, the filtration media holds the impurities. The size of impurities that can be filtered out depends on the filter’s capability.
For example, some filters can filter particles of sizes about 5 – 20mm, while others are used for suspended and dissolved particles.
Drying
Drying is a method of removing water or moisture from the liquid substance after the filtration process. Drying is performed because some APIs are used in solid form, and the liquid state must be converted to a solid state.
The drying must be designed or performed optimally so that the residual substance contains accurate moisture and solid substance ratio.
Some equipment used for this purpose includes the following.
Fluid Bed Dryer – FBD only removes moisture from a solid substance. FBD passes hot air through the powder product bed contained in a product container. As the air passes, the powder becomes suspended and moves freely throughout the perimeter of the product container. Since powder floats in the air, it resembles fluid. This powder condition increases the thermal contact, resulting in optimum and more efficient drying than other drying forms.
The hot air removes the moisture and is continuously monitored through a moisture analyzer. When the moisture level drops to the desired level, the drying process stops, and the product is ready for the next processing stage.
Radiative Drying: This method works by removing the moisture of a solid substance through radiation, and no physical heat source is utilized to remove the moisture. The heat virtually travels and comes in contact with the product, performing the desired heating action. A common form of radiation is microwaves ranging from 10mm to 1mm.
Spray Drying: Spray drying removes moisture from the liquid form. The liquid to be dried is sprayed in an enclosed container in which hot air is continuously sprayed through the appropriate nozzle. As soon as the liquid is sprayed, the hot air immediately removes moisture from the liquid substance, and they are converted to solid form.
The liquid is sprayed until the required amount of liquid has been dried.
Freeze Dryer: A Freeze dryer removes moisture from the liquid by freezing the liquid and then removing water from the frozen state. The drying takes place under vacuum conditions.
The liquid, filled in vials, is kept in a freeze-dryer chamber and then vacuumed. Then, it is frozen at a lower temperature, and the drying phase starts.
Drying continues until the desired level of moisture evaporates from each vial. After drying, powder cakes are left behind in vials, which can be used for their purpose.
Crystallizer
Crystallizer is an equipment that converts solid particles into crystal form. The main reason for the crystallization process is that most solid particles have low solubility in water, which can cause difficulty during the drug manufacturing process. The solid form is converted to crystal to cope with this difficulty.
Crystallization occurs when a product solution is mixed with a solvent or chemical to alter its pH or solubility.
Crystallization is carried out by mixing products at a specific speed and temperature, performed in reactors, as described previously.
Packaging
Packaging is the final stage in API manufacturing, where the final finished API product is packed in packaging material. The most common packaging material is drums because APIs are required and supplied in bulk quantity, which a drum can easily provide.