Remote monitoring in pharmaceutical industry is getting traction because of its unique advantages that help pharma manufacturers achieve their quality, regulatory, and market goals. This article discusses remote monitoring in pharmaceutical industry, how it is implemented, its advantages, and its types.
Remote monitoring in the Pharmaceutical industry is the byproduct of new technology and innovation in communication, rapidly finding its way and shaping the pharmaceutical industry landscape. It enables the pharma industry to monitor a system or process without being physically present at the target location and to collect relevant data.
Additionally, remote monitoring optimizes the production process by utilizing the collected data for various purposes, such as maintenance, production planning, and future forecasts.
What is remote monitoring in pharmaceutical industry?
Remote monitoring is a system through which any process, equipment, area, instrument, and entity (that has any relationship with pharma processes) can be monitored with the help of electronic components and communication systems. The remote monitoring system collects raw data and sends it to the central controller, server, or computer for processing to extract useful information.
The server, controller, or computer comprises a software system that applies various algorithms to make the information presentable for human analysis and decision-making. The remote monitoring system is automated, i.e., there is no human involvement in data collection, type, frequency, and format.
Typically, remote monitoring uses multiple components that can vary depending on the monitoring system. However, it can be divided into Sensors, controllers, Software, and Communication systems.
- Sensors or instruments collect relevant data, such as the target area’s temperature or humidity. Since these must be able to communicate via the latest communication protocols, sensors used in modern-day remote monitoring are called Smart Sensors.
- The controller processes the data collected through sensors to extract useful information.
- The software contains various algorithms to be applied to the information and make decisions such as satisfactory, Pass, Fail, or Error.
- Communication system: The Internet is used as a communication system that requires a dedicated communication protocol. It provides communication between the field device and the central computer or server. It enables transferring data from source to destination without any loss.
The main benefit of remote monitoring is that the entire process is automated and does not require human intervention. It also enables monitoring and collecting data on facilities where equipment is located across a location that is difficult for humans to monitor and manage.
IIOT – the driver of today’s monitoring
The main driver of today’s remote monitoring system is that the information is sent over the Internet through appropriate communication networks such as Ethernet or Cellular. It can be visualized through the Internet and does not require any dedicated hardware or software. Instead, any computer or mobile device connected to the Internet can see it with proper authorization and security credentials.
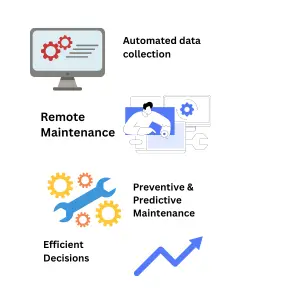
Importance of remote monitoring in pharmaceutical industry
Let’s discuss the importance of remote monitoring in the pharmaceutical industry
No manual data gathering
The first and foremost advantage is that it eliminates manual data collection of the instruments and sensors and provides a system that can be genuinely regarded as an automated system. The data is automatically collected, transferred, and stored in a relevant computerized format.
In traditional methods, the physical variable is monitored and measured by an instrument or sensor in an automated manner. Still, humans collect the data from these sensors and reproduce it in a manual manner, generally on paper. Without centralized remote monitoring, installing an automated data collection can only be done individually, which becomes costly and necessary to integrate with an existing system.
Reproducing data from sensors or instruments is prone to errors, such as human error, irregular frequency, and storage problems.
Preventive and Predictive Maintenance
Remote data collection can enhance the Maintenance of equipment installed in the facility through preventive and predictive maintenance
Preventive Maintenance: it aids in executing preventive Maintenance by providing information about the running hours of a machine. This information can be utilized to enhance the efficiency of preventative Maintenance by modifying the maintenance frequency; it also enables the implementation or changing of the checklist for Maintenance.
Predictive Maintenance: Data collected by remote monitoring can be used to implement predictive Maintenance that works by planning the Maintenance of a component that is near to breakdown or fault
Helps to make efficient decisions
Remote monitoring provides accurate data about the machine’s performance that can be used to make efficient decisions regarding market forecasts, production planning, and supply chain management.
Remote Maintenance
Remote monitoring allows the implementation of remote Maintenance and troubleshooting for a machine. In this application, the maintenance team can remotely access a machine and troubleshoot without physical presence. It analyzes the data collected and can provide solutions to the maintenance team present at the site.
Remote Maintenance is beneficial for cases where the equipment manufacturer is far from the pharma manufacturer. Remote Maintenance can save time and cost associated with the travel.
How remote monitoring in pharmaceutical industry is implemented?
In the pharma industry, remote monitoring is employed at various levels, which can be commonly divided into the following
- Process-based
- Equipment based
- Facility based
Let’s briefly discuss each of the above.
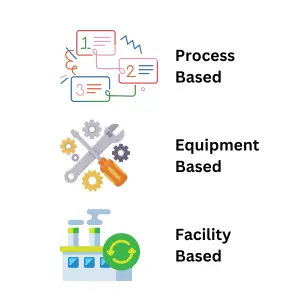
Process-based
Process-based monitoring means monitoring a process related to pharma product manufacturing that has a direct impact on the product or a manufacturing process. Examples include packaging operations and washing containers. In this application, all critical values are measured and sent to a remote controller to monitor and detect errors or faults.
For process-based monitoring, sensors are installed across all the critical steps involved in a process that records all vital variables. These values are then sent to the central controller for analysis and monitoring.
An example of process-based monitoring includes a filling process, which is monitored for variables such as fill volume, pressure, and sealing system.
Equipment based
Equipment-based remote monitoring means collecting machine-related data and sending it to a remote computer or server to monitor its performance. The equipment-specific variables include speed, temperature, pressure, errors or faults, production report, and product level in a hopper or container.
The purpose of equipment-based is to monitor machine performance through various models. Equipment monitoring allows in-depth analysis of the machine’s performance, working, current and output status, and production records.
An example is predictive Maintenance, which continuously monitors the status of components such as motors, oil, gearboxes, and different mechanical structures. The software constantly monitors these variables to predict breakdown by the built–in algorithm.
Other parameters specific to equipment include breakdown & downtime, events, faults, and alarms.
Facility based
In facility-based remote monitoring, all area or facility-dependent variables are monitored. Usually environmental and safety-related. Facility-based variables directly affect the product, process, and equipment working in the area.
An example is the area temperature and humidity critical to product, process, and equipment performance. These parameters are remotely monitored and sent to the central controller for analysis by the software. It alerts and raises the alarm if these variables deviate from the acceptable limits.