Instrumentation in pharmaceutical industry senses physical variables and converts them into electronic or electric signals for pharma equipment to execute their operations. This article discusses instrumentation and its different types.
Instrumentation in pharmaceutical industry senses various physical variables and converts them into electrical/electronic signals for pharma equipment. Their main task is to collect data about the process performance, which the main controller then uses to execute various operations. Common instrumentation in the pharmaceutical industry temperature, pressure, Flow, and levels sensors.
Automation in pharma equipment relies on the instrument used in pharmaceutical industry to make correct and timely decisions. If these pharma instruments are not appropriately selected or have become faulty, the machine will not operate satisfactorily.
What is Instrumentation in pharmaceutical industry?
Instrumentation measures various physical variables and converts them into an equivalent electrical/electronic signal. These signals are then fed to different controllers that can understand these signals to execute multiple manufacturing operations.
An instrument has different parts, depending on the functionality and application. However, they can be categorized into three main components – Sensing Element, Conditioning Circuit, and Output Connector.
- Sensing Element: The sensing element feels the physical variable, such as temperature and pressure, and converts it into an electrical signal. The electrical signal at this stage is variable, un-conditioned, and very small in value. It cannot be used to process information and requires conditioning before external controllers or circuitry use it.
- Conditioning Circuit: Signal from the sensing element goes into the conditioning circuit. It applies various algorithms, such as Gain to convert it into a form usable by an external controller or Programmable Logic Controller – PLC.
- Connectors: After the electrical signal is conditioned to a form that an external controller can effectively use, it goes into connectors. These connectors interface the instrument to an external controller or circuitry.
Types of Instrumentation in pharmaceutical industry
There are various instrumentation in the pharmaceutical industry used for different physical variables. The selection of instrumentation depends on the manufacturing process. If a manufacturing process requires temperature, its corresponding instrument is used. Similarly, for every physical variable, its corresponding sensor is used.
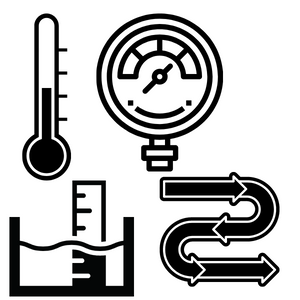
Some common variables for which process instruments are used in the pharmaceutical industry are as follows.
Temperature
Temperature is the most common physical variable used in the pharmaceutical industry. It is used in processes that require a specific temperature for their execution.
Two types of temperature sensors are used in the pharmaceutical industry – RTD and Thermocouple.
- RTD (Resistance Temperature Dependent): These sensors are made up of material that uses resistance to represent input physical variables. The resistance is directly proportional to the temperature value, i.e., resistance increases as the temperature increases. RTD sensors are used for applications that require a low-temperature range to execute a pharma process.
- Thermocouple: These sensors combine two different metallic materials. At the junction of these metals, voltage is induced in the microvolt range. This voltage is directly proportional to the temperature value. They are often used for applications that require a high-temperature range.
The pharmaceutical industry uses temperature sensors in the following process and equipment.
- Sterilization equipment such as Autoclaves and Dry Heat Sterilizers. These equipment require specific autoclave temperature values for sterilization; temperature sensors are used to achieve, control, and monitor the desired value.
- Temperature sensors are also used in pharma vessels to manufacture products and store other liquids at a specified temperature level.
- In the granulation section, certain products require specific temperatures in the drying stage.
- Pharma HVAC system uses temperature sensors to control and maintain specific temperature levels in different areas of the pharmaceutical facility.
- Packaging machines such as blistering machine in pharmaceutical industry use temperature sensors to control and maintain specific temperature levels during various processes.
Pressure
Pressure sensors are used to measure pressure in pharma equipment for various processes. Like temperature, pressure is applied as a part of the process requirement, and the process cannot execute if the correct pressure is not used.
Different physical mediums can be used to apply pressure, such as use of steam in pharmaceutical industry, Compressed Air in pharmaceutical industry, or water. For each physical media, a different sensor is used. For example, a pressure sensor for steam cannot be used for compressed air or water.
There are different types of pressure sensors for different processes and applications. Some common pressure sensors used in the pharmaceutical industry include the following.
Absolute Pressure
Absolute pressure is the value of pressure that is not affected by atmospheric values. It consists of a diaphragm exposed to pressure and vented at another side. The vented side is exposed to an absolute vacuum chamber which is permanently sealed, which prevents the effect of the atmosphere.
Differential Pressure
Differential pressure sensors measure the difference between two pressure levels. It requires pressure input from two different locations. The internal mechanism calculates the difference. The differential pressure is then used for their specified applications.
Vacuum Pressure
Vacuum pressure measures the vacuum in a closed container or chamber. Vacuum pressure means pressure below the atmospheric value and is used in applications requiring emptying containers for practical process completion.
Some process equipment in which Pressure sensors are used includes Autoclaves, Freeze dryers, and Air Handling Units.
Flow Sensors
Flow sensors detect and measure the amount of fluid flowing through an enclosed cross-section. They are used in equipment and processes requiring precise fluid control during product manufacturing processes.
Examples of some processes which require flow sensors include the following.
- Pharma manufacturing process
- In injectable packaging, flow monitors are used to accurately fill the amount of drug in Vials and Ampoules.
- Flow sensors monitor the amount of liquid filled in a container for Oral Solid Liquid.
- In the Pharma HVAC system, flow monitors are used to monitor the airflow in an area by installing airflow sensors in the desired area.
- In Water Treatment Plants, flow sensors are used to monitor and control the flow of
- Incoming raw water
- Chemicals
- Water, as it passes through different stages of treatment
- Output purified and Distilled water.
- Output steam in the steam generator.
Level Sensors
Level sensors monitor the level of a liquid in a container. The main controller, such as a Programmable Logic Controller, uses the output of the levels sensor to keep the fluid level in a container. If the fluid decreases below the desired level, it operates the pump or gives an indication.
Some processes and equipment that use level sensors include the following.
- Level sensors are used in Storage Tanks of Water Treatment Plants. When storage tanks are filled with water up to maximum capacity, it signals to stop the plant to prevent water from overflowing. Level sensors also signal the circulation system to start/stop.
- Liquid filling machine use level sensors to monitor the fluid quantity in the hopper. There are two objectives of the level sensor.
-
- The first objective is to fill the liquid in the hopper. When liquid drops below the set point, it activates the hopper filling system to make up the fluid level.
- The second objective is to stop the machine when liquid falls below the dead point because levels below the dead point will affect the filling rate and empty the hopper.
Installation Configuration
Like other industries, pharmaceuticals have two configurations for Installing a Level Sensor – Point Level and Continuous.
Point Level
In the point-level configuration, the sensor detects the liquid level of a particular point. When the liquid reaches this point, it gives the main controller a binary (ON / OFF) signal. This is used in an application that only requires an ON / OFF function.
Point-level sensors are also used as a safety mechanism to prevent fluid spill if other level safety control mechanisms fail.
Continuous level Monitoring
Continuous level monitoring gives the real-time value of fluid level in a container. They generate electronic signals corresponding to the liquid level. As the liquid level increases, the value of the electronic signal also increases. Similarly, if the liquid level decreases, the value also decreases.
Level sensors generate two types of electronic signals – 4 to 20mA and 0 to 10V. It means the minimum level equals 4mA or 0V, while 20mA or 10V equals to maximum level.
Types of Level Sensor
There are two significant types of level sensors in the pharmaceutical industry- – Contact and Contactless.
- The contact level sensor comes in direct with the liquid. It has a long rod calibrated to the minimum and maximum of the container. Different points of rods indicated different levels in a given container.
- Contact Less level sensor does not come in direct contact with the liquid. Instead, it is installed at a distance from the maximum capacity of a container. It electronically measures the liquid level by sending and receiving the electronic pulse.