Blistering machine in pharmaceutical industry is an essential element of the pharmaceutical industry, in packing department. This article discusses blister packaging machine, their parts and various types.
Blistering machine in pharmaceutical industry is an essential element of pharmaceutical industry, used to pack pharma products. The blister machine carefully places the pharma product in between two packaging materials. The packaging materials are then sealed together so that it becomes air-tight and protects from foreign bodies such as moisture and particles. The final stage cuts the Blisters into the desired length and shape.
Blister packaging machine consists of various sub-sections performing their respective functions. The feeder feeds the blistering product through the feeder from one side of the machine. It then travels through these different stations or sections and finally emerges from the machine in packed blister form.
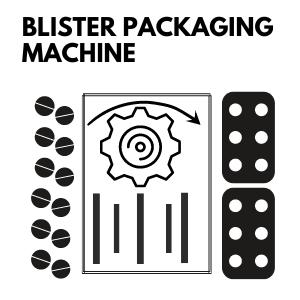
The machine runs through a centralized automatic control system such as a Microcontroller or Programmable Logic Controller to execute all the related functions without human involvement. The main controller controls all the main and secondary functions. The machine uses various sensors to monitor operation and to signal the main controller.
Motors powers various motions, controlled through the main controller.
Motions are usually Linear and Rotary, depending on the machine’s functions and type. There are also mechanical components such as Gear Boxes and cams for various functions.
In the pharmaceutical industry, blister packaging machines pack the following product types
- Tablets
- Capsules
- Ampoules
- Vials
Parts of blistering machine in pharmaceutical industry
Blistering is a process that involves many small functions. Many individual stages perform these small functions, and the output of each stage is dependent on its later stage.
Let’s look briefly at parts of the blistering machine in pharmaceutical industry.
Unwinding Station
The unwinding station is the first station, carrying the forming foil. It unwinds the foil as required by the later stages. There are two mechanisms of foil un-winding – Automatic and Manual.
In an automatic mechanism, a sensor continuously detects the tension of the foil. When there is tension, it indicates the requirement at a later stage. In that case, a motor rotates and automatically unwinds the foil. The sensor also detects the required quantity of foil to be unwound. If sufficient foil has been un-winded, it stops the unwinding process. This un-winding process then continues for the rest of the blistering process.
In the manual process, foil is unwinded by the force of the machine’s forming station.
Forming Station
The foil from the unwinding station travels into the forming station, which contains mechanical assemblies to create cavities in the foil. The cavities take the form of the desired tablets with the help of mechanical assemblies, such as Punches.
If the machine is ALU – ALU, foil is directly punched into the mechanical assembly with pressure, without heating.
If the machine is PVC – PVC, the foil is heated to soften it. Heating helps in cavity formation. After heating, a vacuum creates the cavities.
Filling Station
In the filling station, tablets or pharma product fills the cavities. A vibrator containing the Pharma products moves the product forward, commonly in a circular direction. From the vibrator, it travels into the narrow chute or channel, which ends up in these cavities. As the vibrator vibrates and foil moves forward, pharma product from the vibrator through the channel or chute is automatically placed in the cavities.
Sealing Station
In the sealing station, the upper foil seals the lower foil. A heating element seals the foil, and its temperature depends on foil and product characteristics.
Cutting Station
In the cutting station, a blister of appropriate size is cut by mechanical assemblies such as a cutter jaw with the sealed foil in between. When the sealed foil is appropriately positioned between the jaws, they are activated, and blisters of appropriate sizes are cut together.
Types of blistering machine in pharmaceutical industry
There are various types of blistering machine in pharmaceutical industry, the selection of which depends on the product being packaged, process requirements, and market demand.
Blister Packaging Machines can be categorized according to two main factors.
- Machine structure
- Packaging Material used by the machine
Let’s look at briefly different types according to each category
Machine Structure
Machine structure means arranging the blister machine’s main parts, such as Forming and Sealing Station. Commonly, blister machines can be categorized into three types according to the machine structure
- Roller Type or Rotary
- Plate Type
- Roller Plate type
Roller Type or Rotary
The blister’s forming station and heating station are circular in the roller-type blister machine. They continuously move in a rotary direction during machine operation.
Packaging material continuously passes over the circular-shaped forming station as it constantly rotates. At the same time, it creates pockets in the packaging material.
Similarly, the sealing station is also circular and continuously rotates. Filled cavities with the upper packaging material pass between the station assemblies. The packaged material is sealed in a rotatory position.
Since both station continuously rotates during their operation, they consume less heat and have less heating efficiency. Additionally, they have high speed and result in increased output efficiency.
The rotary-type blister machine suits small to mid-sized products such as tablets and capsules.
Plate-type blister machine
In plate-type machines, heating and sealing stations are plate-shaped and have linear, intermittent motion during machine operation.
Packaging material is placed over the forming station during forwarding motion through different mechanical components. Initially, the packaging material is aligned with cavity-forming assemblies. Then forming station activates to create cavities of desired size and shape.
Similarly, packaging material filled with product and wrapped in the upper material is placed on the heating station. The machine stops to align the packaging material with the heating station. Finally, the upper portion of the heating station lowers itself to seal the packaging material.
During the machine operation, motion is not continuous. Machine advances and stops to carry out all the related functions such as forming, filling and cutting
Packaging Material used
Another method to categorize Blister packaging machines is using Packaging material for packing purposes. Commonly, there are two types of packaging material for pharma product packaging – Aluminum and PVC.
Aluminium and PVC are used in two different combinations, and their combination defines the category of the blister packaging machine.
ALU – ALU Machine
In ALU – ALU machine, the aluminium foil is used as a forming foil, in which cavities for inserting tablets are formed. Aluminium foil is used as a lidding or upper foil to seal the blister.
For creating cavities, punches of the required size are inserted with pressure against the aluminium foil without using the heater. Punches then create cavities of desired shape and size. After cavities formation and product insertion, the blisters are then sealed with the aluminium foil, and further process executes to complete the blistering process.
ALU – PVC Machine
In ALU – PVC type, aluminium is used as forming foil to create cavities for tablets, and PVC is used as a lidding foil to seal the blisters.
PVC – PVC Machine
In PVC-PVC type, PVC is used as a forming foil to create cavities for pharma products. These types require a high temperature to soften the PVC, and a vacuum is used to create the cavities.
PVC is also used to seal the packed pharma products for lidding foil.