A pharmaceutical dust collector removes airborne particles in pharma production areas, especially in Oral Solid Dosage. Learn in detail about its Importance, different parts, and working.
A pharmaceutical dust collector is common in Oral Solid Dosage sections of the Pharmaceutical Industry. They are used in processes that generate and use powder in any manufacturing stage.
The design and construction of a pharmaceutical dust collector depend on many factors, such as dust type, area, and manufacturing process.
What is a pharmaceutical dust collector?
Pharmaceutical dust collector collect dust particles that have escaped during the production process and store them in a collection bin or hopper. These small particles can pass the opening of any size and shape. As a result, these particles can become products and personnel.
The air discharges into the environment after separating the particles from the air. The filters remove the particles and make the air safe to release in the environment.
Dust Collectors are used with pharma oral solid processing equipment such as tablet compression and Blister Packaging Machines. Their operation must be synchronized with the attached manufacturing machine and compatible with the output rate.
Production is prohibited if the machine’s dust collector is unavailable or faulty.
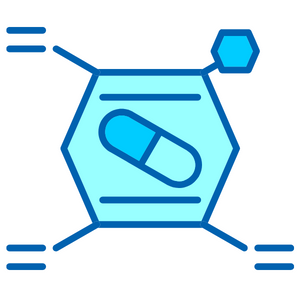
Parts of pharmaceutical dust collector
Some important parts of Dust Collector are as follows
Air Intake
Air intake is the opening in the pharmaceutical dust collector that collects dirty or powdered air from the production area. It connects the exterior of the dust collector to the filter housing.
Ducting system of the area connects the air intake part to the production process area. These ducts transfer the air from the production area to the dust collector intake section.
Filter Housing and Filters
The filter housing is the mechanical assembly in which filters are installed. The intake air passes through filters in the filter housing to remove the powder particles.
Commonly, a Cartridge filter is used in a pharmaceutical dust collector.
Cartridge filters have high efficiency than other types, such as baghouse. Cartridge filters have a larger surface area, have high efficiency near HEPA filters, and can easily filter out fine and tiny particles.
The access door is provided in the filter assembly to access the filters for maintenance.
Hopper
Hopper is the collection point of dust particles released from the filters. It is supplied with an airlock mechanism to prevent the re-circulation of dust particles into the dust collector.
The collected powder starts circulating if air locks are not provided. It will increase the dust load and negatively affect the dust collector’s performance.
Blower
The blower creates a force to extract and collect dust from the area. The blower can be top-mounted or ground-mounted, depending on the design requirements.
The size and capacity of the blower depend on the air extraction requirement.
Clean Air Exhaust
Clear air exhaust releases clean air from powdered particles into the environment. The exhaust is connected to the ductwork to guide the air to its respective exhaust point.
Ducting
A separate ducting system connects the dust collector to the production area since the dust collector is placed in the technical area, outside the pharma production area.
Control Components and Instrumentation
Variable Frequency Drive
VFD is used to control blower operation. The main controller sends a signal to VFD to activate functions such as Start, Stop, Speed Increase, and Decrease.
Differential Pressure Monitor
Differential pressure systems continuously monitor the differential pressure across filters. The main purpose of differential pressure monitors is to indicate when the dust on filters has reached its maximum capacity, and filters need cleaning or changing.
Increased pressure values indicate large quantities of dust on filters, and action is required. Otherwise, it can decrease the efficiency of filters.
Working of a pharmaceutical dust collector
Many variants of dust collectors differ in operation. However, the following is the common working principle on which dust collectors are designed and constructed.
- The dust collector collects the airborne particle. The particles travel into the dust collector through the filter section.
- Heavy dust particles settle down and are collected in the hopper.
- Lighter particles remain on the filter.
- The clean air escapes through the exhaust into the environment.
- When filters become heavy, they are cleaned manually or through an automatic system.
- The manual method moves a lever, which moves the filter housing. As the filter housing moves, powder particles drop from the filter and are collected in the hopper.
- In automatic mode, the filter housing is automatically moved through instruction from the main controller, which also causes the powder particles to drop. The automatic movement can be set according to a given time or programmed to the values of differential pressure monitors.
Area of application for Pharmaceutical Dust Collector
As mentioned above, dust collectors are used to collect powder in the pharma industry, and their main application is where the powder is the main dosage form.
Some departments of the pharma industry where dust collectors are common include the following.
Tablet Compression Department
The tablet compression department compresses the powder into tablet form using a tablet compression machine. A powder often escapes from the hopper and machine parts during tableting, such as the machine feeder and ejection cam.
Tablet Coating Department
In the tablet coating department, tablets are coated with different chemicals for various therapeutic effects.
Powder escapes into the environment during tablet transportation. Additionally, the tablet’s surface also releases powder before coating.
Fluid Bed and Spray Drying
Fluid Bed Drying is the process in which bulk powder quantitates are dried. The equipment is called Fluid Bed Dryer, and its drying technique makes the powder flow like a fluid.
During its drying process, the powder can become airborne during powder transfer into the area and equipment, during the drying process, from different equipment parts.
Granulation and Bending
Granulation converts powder into granules form with the help of dry and wet mixing. The powder can escape from different machine parts during the powder transfer and production process.