There are various types of calibration in pharmaceutical industry, depending on the instrument types. This article discusses some types of calibration in pharmaceutical industry.
As mentioned in the previous article, calibration verifies the output of a measuring instrument against standard values. It helps detect and rectify faulty instruments. Additionally, calibration is critical for various regulatory bodies, such as the FDA and the ISO. There are different calibration in pharmaceutical industry, depending on the instrument being used
The pharmaceutical industry uses different measuring instruments and devices for different processes in product manufacturing. The effectiveness of a pharma product and process depends on the performance of these measuring instruments. The entire process can become erratic if any of these instruments malfunction.
Additionally, calibration is used with other maintenance strategies to prevent any errors in these instruments during production.
Types of calibration in pharmaceutical industry
Every measuring instrument in the pharma industry has its own calibration procedure, which cannot be repeated or performed for other instrument types.
Let’s look at some common types of calibration in pharmaceutical industry
- Temperature Calibration
- Pressure Calibration
- Speed Calibration
- Weighing scale calibration
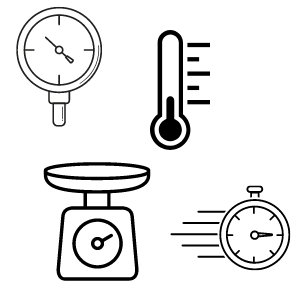
Temperature Calibration
Temperature is the most used physical parameter in the pharmaceutical industry, and its application can be found in areas such as Manufacturing, Sterilization, and Packaging. Without temperature, these processes cannot be executed with the desired product properties.
Examples of pharmaceutical equipment that use temperature as a part of process requirements include Autoclaves, Dry Heat sterilizers, Blister Packing Machines, and manufacturing Vessels.
In the equipment mentioned above, temperature sensors are used for two applications.
- Different values of temperatures are used to achieve different process stages during a process. A difference between the actual temperature value and the sensor’s output will negatively impact the procedure.
- Temperature sensors are used in automatic control systems to maintain the temperature in the required range, such as in autoclaves, where temperature sensors and instruments control autoclave temperature.
In both cases, the performance of a system depends on the temperature-measuring devices. If the output of temperature measuring devices is accurate, they will accurately help in executing the process. Otherwise, the temperature control function will not work accurately.
Various types of temperature sensors are used in the pharmaceutical industry, but common types include Resistance Temperature Detectors – RTD and thermocouples.
Advantages of Calibration
Advantages of calibrated temperature measuring devices include but are not limited to
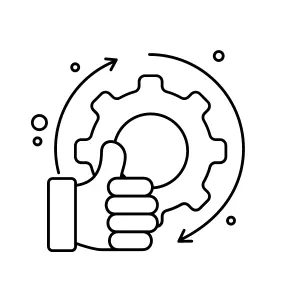
- Accurate monitoring of the production process
- They enable personnel to achieve the production process safely
- Calibration help in fulfilling regulatory requirements
Calibration procedure
Temperature calibration is performed by simulating different temperature values and observing the output of the temperature sensor. The value of the simulated temperature depends on the temperature sensor’s range and process requirements.
Commonly, three values are simulated, and personnel records the actual sensor’s reading. Calibration is passed if the difference between the sensor’s output and the simulated temperature lies within the range. Otherwise, calibration fails, and maintenance personnel must rectify the temperature system.
Pressure Calibration
Pressure is another common and frequently used physical parameter in the pharmaceutical industry. Different equipment uses certain pressure of various fluids to achieve a certain product characteristic and specific process stage.
For example, in some cases, the pressure of a certain fluid is required to manufacture a product, which cannot be accomplished without it. The pressure parameter is also used in filling operations where specific pressure of fluids such as Nitrogen and Compressed Air is used to execute the filling process. Similarly, specific pressure is required to perform various tests on a given sample in the quality department.
Production and quality personnel also frequently monitor pressure for critical areas such as Clean Rooms. As a result, pressure monitoring is important in maintaining area characteristics necessary for achieving the pharma processes.
Various pressure measuring devices are used to monitor and detect the required pressure in all these cases. The success of the entire process depends on the accurate working of these measuring devices.
Calibration helps to keep these pressure-measuring devices in working condition and enables concerned personnel to detect any fault before it seriously affects the ongoing process.
Calibration procedure
Pressure calibration is performed by applying a known pressure value to the device under test. The pressure is applied through a portable pump, which indicates a separate indicator.
The process pressure value is recorded and compared with the applied value (on a separate indicator). The difference between the applied and measured pressure is noted and recorded. If the difference lies in the acceptable limits, device calibration is passed. Otherwise, it failed, and it must be replaced or rectified.
Some pump manufacturers combine all the calibration requirements in a single package for easy calibration.
Speed Calibration
Speed calibration verifies the speed of various systems that rotate or move per minute. Different motors usually perform motion in pharmaceutical equipment. In addition, other mechanical assemblies and attachments transform rotary motion into linear motion.
A common application of speed in pharma equipment includes the equipment speed, which defines the equipment’s capacity. The equipment’s speed is indicated on the machine indicator, which production personnel use to increase or decrease the equipment’s speed.
Calibration procedure
Speed is calibrated and verified by counting the revolutions per minute of a given system externally, usually through a tachometer. The resulting counts are then matched by the local indicator installed on the machine.
Weighing Scale Calibration
The weighing scale is the most commonly used instrument in the pharmaceutical industry in their production and quality department. They precisely weigh different chemicals for use in the testing and manufacturing process.
In most cases, weigh scale manufacturers provide an in-built calibration procedure with the scale. The only requirement is an accurate and calibrated weight during the calibration procedure.
For calibrating the weighting scale, place the weight on the scale and follow the procedures described in the operating or maintenance manual. When calibration is successful, the scale signals it on the indicator and can be used for normal operations. Otherwise, an alarm appears on the indicator, and the scale cannot be used for further operations.