Clean Room in pharmaceutical industry is used by pharma companies to ensure product safety. This article introduces Clean rooms, characteristics, and what environmental parameters are monitored.
Clean room in pharmaceutical industry are enclosed area that provides controlled environmental conditions for various critical processes in a different industrial environment. Their primary purpose is to provide a particle and contamination free environment for manufacturing processes to prevent contamination.
They can block particles such as dust, airborne particles, and chemical vapours to purify the air inside the clean.
It is also possible to control air parameters such as temperature, humidity, and flow inside clean rooms through various automation and instrumentation systems. Thus clean rooms enable control of the environmental parameters in a way that best matches the requirements of an ongoing process.
Clean rooms are an integral part of many industries with strict environmental requirements. Examples include pharmaceuticals, semiconductors, and medical devices. If clean rooms are not used in these industries, it can severely affect the process and will destroy the output product.
Clean room in pharmaceutical industry
Clean rooms in pharmaceutical industry provide suitable environmental conditions for manufacturing sterile products, such as injectables, which have a high degree of purity requirement. If the desired controlled area characteristics are not provided, the product becomes hazardous and cannot be used for human consumption.
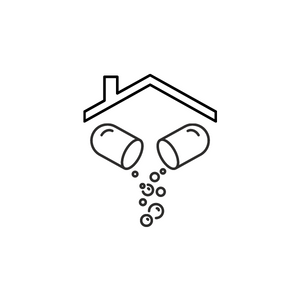
In the pharmaceutical industry, clean rooms are also used to provide controlled environmental conditions to perform specialized tests such as sterility. These tests monitor the product integrity during different phases of the product manufacturing life cycle.
Characteristics of
Clean room in pharmaceutical industry
In the pharmaceutical industry objects such as Humans, Equipment, and Furniture is a common sources of particle generation. In addition, some pharmaceutical processes require a high degree of purified air to execute their operations safely.
Clean rooms help create a safe and particle-free environment, essential for critical pharmaceutical processes.
Air Filtration
Clean room in the pharmaceutical industry uses HEPA filter, having an efficiency of 99.97% to filter out particles of size up to 0.3µm. These tiny particles cannot be seen by the naked eye but can cause a severe hazard to manufactured medicines. These particles also carry airborne diseases, which can cause contamination of the surrounding air.
Air Flow
The air inside a clean room must be regulated and must follow a uniform pattern of flow. Additionally, if for some reason, particles penetrate the cleanroom, the airflow should carry the particles out of the cleanroom.
It is implemented by controlling the flow of air inside clean rooms in a way that
- A complete cycle of air volume flows out of a clean room
- At the same time, a complete cycle of air volume flows inside the clean room through a HEPA filter.
A complete cycle of air volume going outside and replacing it with fresh air is called Air Changes. The requirement of air changes per hour depends upon the process being carried out, and can be adjusted according to the needs and requirements.
The Air changes prevent the contaminants from settling inside a clean room and are immediately removed from the clean room before they reside on any object.
Classification of
Clean room in pharmaceutical industry
Cleanroom classification identifies different clean rooms and divides them based on their ability to remove different-sized particles. Clean room classification is performed to select a proper clean room for a specific process or product.
Clean room classification is defined by different standardization bodies such as the International Standardization for Organizations and the EU. Each standard has its own procedure for classification.
ISO Classification for Clean room in pharmaceutical industry
ISO specifies air cleanliness in terms of the number of airborne particles and is defined in ISO 14644-1:2015 standard. The technical committee that has developed this standard is known as “ISO/TC 209, Cleanrooms and associated controlled environments”.
This standard is based on the particle size of 0.1 µm to 5 µm.
There are nine cleanroom classes, including ISO1, ISO2, ISO3, ISO 4, ISO 5, ISO 6, ISO 7, ISO 8 & ISO 9.
ISO 1 is the purest of all classes, while ISO 9 is the least pure.
Environment monitoring of
Clean room in pharmaceutical industry
Clean room environment monitoring involves continuously measuring different environmental parameters in a clean room to monitor the clean room’s performance, working, and efficiency.
Monitoring enables detecting and rectifying any fault before affecting the process or product.
The monitoring systems use various sensors and instruments to record environmental conditions. If there is a deviation in typical values, it activates an alarm. The alarm alerts the concerned personnel to take necessary corrective actions before the condition becomes hazardous for the product and process.
There are three types of critical parameters that are monitored in a clean room. These are Environmental, Particulate matter and Microbial.
Environmental Monitoring
There are three types of environmental parameters that are monitored
Temperature
It includes the actual temperature of a clean room by placing temperature sensors at different critical locations.
Specific products such as biological require a specific range of temperatures for their manufacturing. Clean room temperature monitoring enables the smooth execution of the production process for temperature-sensitive products.
Humidity
Humidity is measured for executing a smooth production process and ensuring cleanliness inside a clean room. Excessive humidity results in microbial growth, cause corrosion and contaminates the product and other objects.
Excessive humidity also creates condensation, which requires more cleaning than usual. Condensation also causes short-circuit problems in electrical & electronic systems, causing these systems to be damaged.
Differential Pressure
Differential Pressure is the measurement of the pressure difference between two locations.
In clean rooms, differential pressure measurements are used to ensure the correct direction of airflow. Correct airflow direction is necessary to move the contaminants from inside the cleanroom to outside and to prevent the ingress of contaminants inside the clean room.
Particle Monitoring
Particle monitoring detects the size and number of particles inside clean rooms.
Clean rooms are classified according to the type and size of particles allowed inside them. During particle monitoring, if the detector detects out-of-specification particles, it indicates a problem with the clean room. Maintenance personnel can be immediately called to solve the problem.
Microbial Monitoring
It includes monitoring for detecting microbial growth inside clean rooms. This growth can occur at any place inside a clean room, even on personnel and their clothing. Microbial growth monitoring includes the following methods
- Plates exposed at specific locations for a specified time
- Swabs for surfaces and human gowning