There are two methods of manufacturing in the pharma industry – batch and continuous. They both differ in the way the process advances throughout the manufacturing process. This article discusses difference between batch and continuous process and highlights some key differences
Continuous and Batch manufacturing are two methods of manufacturing a product in the pharmaceutical industry. Continuous manufacturing is the latest method developed to reduce time, cost, and resources associated with bath manufacturing. Batch manufacturing is traditional yet proven method of manufacturing a pharma product with safety, integrity, and desired therapeutic properties.
This article discusses difference between batch and continuous process, but first, briefly discusses the Batch and Continuous Manufacturing process.
Batch vs Continuous Manufacturing Process
Batch manufacturing is a conventional method of manufacturing pharma products, where the production process is divided into many steps. Each step is carried out in a separate facility or equipment. The production process advances to its next stage only after the product has passed relevant acceptance criteria. Otherwise, the product remains in that stage. Sample testing is carried out offline, typically in a laboratory environment. Parameters adjustment is also carried out offline by stopping the production process.
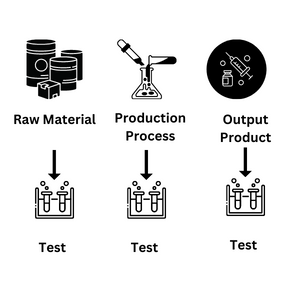
Continuous manufacturing is the latest and most innovative process, eliminating intermediate steps. The entire production process is carried out in a single equipment and facility without transferring the product from one location or equipment to another. Raw material enters the manufacturing equipment and comes out as a finished product in a single go. The production process does not hold or halt for a moment. All the routine sampling, testing, and parameters adjustment are carried out online, at the process location.
Batch vs Continuous Manufacturing Process
Let’s look at briefly how these both processes differ from each other
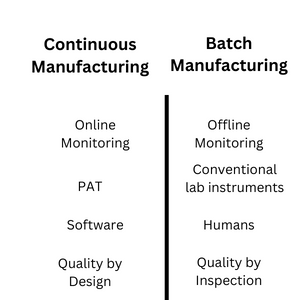
Multiple Steps vs Single Step
Batch manufacturing consists of multiple stages, where each stage is distinct and separate from its previous and other stages. Dedicated facilities or equipment are designed for every stage and cannot be interchanged with facilities or equipment designed for another stage. The process advances to its higher stage only after the output of the preceding stage has passed the relevant acceptance criteria.
Continuous manufacturing is a process consisting of only a single step. Raw material enters the equipment, and from the same equipment, output comes out. There are no intermediate stages, nor is the production process stopped at any stage. All the sampling, monitoring, and quality improvement techniques are carried out during the process without stopping production.
Offline Vs. Online Monitoring
In Batch Manufacturing, process and quality improvement measurements are performed offline, away from the process location, i.e., process equipment. During measurements, the process is stopped until the result are compiled. Production personnel decides, based on results, whether to proceed, stop or repeat the process.
Continuous manufacturing requires online monitoring for process and quality improvements. The measurements are performed at the process location, i.e., at the equipment, without stopping the process. The production continues while processing the results. The system immediately compiles the result at the process location, which is immediately available for further processing.
Conventional Lab Instruments Vs.
Process Analytical Technology
In batch manufacturing, conventional lab instruments perform process and product monitoring. The samples from the process are taken to the laboratory where the instruments are located. Before testing, samples are prepared for the desired instrument, and then the test is executed. The sample result is localized with the laboratory, which must be communicated to the process execution place by a manual system or electronic medium. Examples include Spectrophotometer, pH meter, and HPLC.
Process Analytical Technology – PAT is used in continuous manufacturing to monitor the ongoing process in real-time. This system does not require sample preparation, and the product can be directly tested from the equipment in real time. PAT is a technique for online production monitoring processes associated with different industries, including pharmaceuticals. Process analytical technology allows deviation to be detected in real-time and allows immediate improvement techniques. Examples include in-line particle size analysis to monitor particle size and the output of a continuous solution crystallization process in the pharmaceutical industry.
Humans Vs. Software
In batch manufacturing, Humans decide all decisions regarding samples and the corresponding actions. They decide the sample time, frequency, sequence, and test procedures. Similarly, the decision to implement specific actions, such as changing the chemical concentration, and accepting or rejecting the product, is also carried out by humans. If humans do not intervene or take action, the process will proceed without any improvement or change.
In continuous manufacturing, software analytics such as Siemens Simatic SIPAT is used for monitoring the samples. The software decides all the monitoring attributes, such as sampling time and sample procedures. Similarly, test results are also carried out by the software.
Quality by Inspection Vs. Quality by Design
In batch manufacturing, quality is tested after the process has been completed. Under this approach, quality is injected into the product rather than ensured during production. If the quality attributes are satisfactory, the process advances to its next stage. If, on the other hand, quality attributes are not acceptable, the process is repeated until quality parameters become acceptable. The entire product batch is discarded or destroyed if it is impossible to attain the desired quality attributes.
In continuous manufacturing, real-time process monitoring and control enables quality by design feature, which maintains quality throughout the manufacturing process. It allows the process to automatically adjust various parameters during the manufacturing process to compensate for the desired quality attributes. This reduces time and resources for attaining the desired quality variables and product re-testing. It also prevents scrapping or destroying the entire Batch in case quality attributes are unable to be achieved.